The DFB’s Service Support Centre plays a pivotal role in making the DFB operational 24/7.
“When people hear garage, they think of a small workshop, but this place is much bigger than that and has a lot more roles than just fixing and maintaining vehicles,” A/D/O Martin Cooke explained to me on a recent visit to the Stanley Street site. “That’s no small task in itself, given that there are 115 vehicles in the fleet that need to be maintained and serviced, but we are more than just maintenance: we supply an extensive and comprehensive service that enables the DFB to keep moving on a daily basis. That’s why we are now called the Service Support Unit, rather than the garage.”
As he showed me around the massive store rooms, workshop, decontamination unit, laundry and pharmacy, that point became clear, and while civilians may not even know the place exists, the sheer volume of work done here may be news to some DFB members too.
A few months later, Third Officer John Guilfoyle, who has been overseeing operations here for five and a half years, echoes the thoughts of A/D/O Cooke as he too shows me around. “There is so much to cover here. People joke with us that we do nothing down here. They don’t see it, but they don’t complain about the service support, and that’s a compliment for us. DFB members arrive into their station and have everything they need, everything is working. From our point of view, if we are doing our job well, we usually hear nothing. In many ways it’s the unglamorous part of the operation. The key to it is planning and supply change management, but it’s a very broad role.
“Part of my brief is to oversee logistics and equipment. Our principal function is to offer the support services required by operations – that includes the fleet, equipment, buildings overseen by property maintenance manager Andy Kavanagh, and the maintenance and compliance of our equipment: All the supports that keep the operational show on the road. Our vehicles cover 1.7million kilometres annually, with our ambulance service alone covering in the region of 90,000 calls across 12 ambulances, and those 12 cover 1million kms. Our fire fleet do roughly 35,000 calls, and they would cover about 800,000 kms per year. So, it’s a big operation in terms of fleet.”
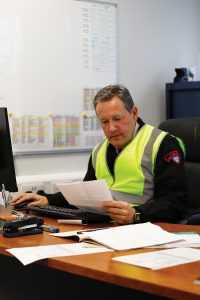
Third Officer John Guilfoyle oversees operations
THE FLEET
While routine checks are done on all vehicles at their stations, the ambulances are brought into the garage weekly, while the fire fleet are brought in every three months, and with more than 4,000 routine repairs done every year, managing this involves a huge amount of planning.
“We have a fleet inspector, who makes out a structured fleet management plan, and that is structured across the fleet annually,” T/O Guilfoyle tells me. “On top of that, all our HGV vehicles undergo CVR testing. In terms of activity, on average we cover around 4,000 non-scheduled repairs that are booked in on a daily basis. If crews at the stations find anything wrong, they report it to us through a central reporting system that comes in here.
“We also manage and maintain in the region of 12,000 pieces of operational equipment, ranging from hydraulic gear to general firefighting tools, hoses, pumps, all the firefighting and EMS gear. Some is done in-house and some by external contractors, which has to be compliant because it is life-critical safety equipment.
“It’s a huge operation that involves a structured plan dictating key performance indicators and key activities we must complete. I have a reporting system that is fed in through the staff here, so at a management level I can see where we are in terms of maintenance, certifications, etc.”
While the amount of work done is immense, there is a relatively small team, all of whom play a pivotal and mostly unseen role for the DFB.
“We have an inspector, five mechanics, a D/O, and five people in our equipment section, so it’s a tight little operation, despite its size,” T/O Guilfoyle says. “We also have two admin staff here looking after accounts and vehicle records – Altona and Noleen – and an accounts section in Tara Street, working in the background, processing more than 2,500 supplier payments and purchase orders per year in the required prompt fashion, and monitoring expenditure. That’s a key function that is often overlooked too, but they are key.”
STORES
Keeping track of the numerous comings and goings of equipment, vehicle parts, stock and consumables would be almost impossible without the proper systems in place, and T/O Guilfoyle shows me around the store rooms to show how this is done.
“We have seen a major increase in the use of IT, which helps produce a lot of management reports and data, which enables us to structure the service in terms of having the right equipment in the right place at the right time,” he tells me. “Our asset management system also helps us to plan in terms of replacing assets, and this also manages testing, servicing, etc, flagging what tests are due and giving us structured reporting. So, if you have 12,000 pieces of equipment, we can key in end of life data, and that enables us to form a strategic five-year plan to see what is coming up this year, next year, etc. If we can project that, we can project the financial requirements. So, certainly, IT plays a big role now.”
Asset Manager A/S/Off Paul O’Toole shows me that is involved. “We take each piece of equipment as it comes in and scan it so that it is added to the system,” he says. “All information about that piece of equipment can then appear on the system – service dates, end of life, any repairs – and the system is automated with colour coding to tell us when it is due to be serviced, replaced, etc. This system, which T/O Guilfoyle brought in a few years ago, is critical to how we operate now.
“Each serial number and code is unique to each piece of equipment, and this is an essential tool to have because we need to be able to monitor all information regarding each piece of equipment in order to ensure they reach safety compliance and are fit for purpose for our members.”
EQUIPMENT
As we walk through the vehicle parts stores, we are met by A/S/Off Stephen McMenemy, who is in charge of equipment maintenance. “Stephen is what we like to call our quartermaster,” T/O Guilfoyle says. “If he is having a bad day, I am having a bad day, because he is key to the operation working.
“When the crews check their equipment on the road or at the station and make out their list of what they need, they send it in by email so that we can get it ready. Stephen deals with all of the stores and stock, and requests for equipment. There’s a balance between having all of the equipment that is needed, and not having too much that it has to be disposed of. It’s a fine line.”
A/S/Off McMenemy tells me that like with any major operation, logistics is hugely important. “This place makes sure that everything is 100% all of the time, that every vehicle has everything it needs on it, from a crowbar right up to essential lifesaving equipment. We have a very good stock management system called Imprest Stock. It’s like a minibar in a hotel, when you take something off the shelf it is recorded on the system, and it works very well because we have never run out of parts.”
PHARMACY
Moving into the main warehouse, I see the shelves are filled with everything from stretchers to HGV wheels and pallets of water, but to the side is the new dedicated pharmacy run by FF/P Ken Kelly, which distributes controlled medications to the ambulance crews.
“In line with Clinical Practice Guidelines, there are more drugs a paramedic can use, so we have quite a lot of medications in the supply chain that have to be managed, and that has a lot of requirements in terms of dates, storage, etc,” T/O Guilfoyle says. “The medicines have to be kept separately from other supplies, with some of the medications stored at specific temperatures. Shelf life has to be strictly adhered to, so again everything is put onto a management system by Ken, which also keeps track of what is coming in and going out.
“He receives all orders for medication and makes sure there is nothing on the list that they are not authorised to have, so it is an important part of the job.”
A/S/Off McMenemy adds: “The pharmacy is really well run, and it has to be. Everything needs to be in the right place and records need to be kept immaculately. Ken is great at that. He set it up in 2018, and has been working wonders ever since. When he is off, we have to try to keep to his high standards, which is a tall order.”
GARAGE
We go down to the garage workshop, where the team are busy running checks on a HGV, and while foreman Fran and John “Horace” Fitzgerald oversee things, mechanic Keith Lambert is pushed into frame for a photo. “Keith is a top mechanic,” S/O McMenemy tells me. “We still call him the apprentice because he is the newest here, even though he has been here a good few years now. He and the other mechanics have to work to very high standards, and you can see that it is a multi-faceted job they have.”
PPE
Maintaining equipment includes all of the DFB PPE gear, and T/O Guilfoyle tells me that they now have one of the leading PPE management systems in Europe. “We have a database that tells us what we need to know about every garment – where it is, what conditions it has been subjected to – and we do the washing and maintenance here at our dedicated laundry facility to ensure they all comply to the standards in place for structural firefighting PPE.
“We encourage our members after any heavy-duty incident to send their PPE back. Everybody has a spare set, so for their long-term health we don’t want people wearing smoky gear. It gets a certified wash, dry and inspection. Our expert in garment care from Hunter’s, Tatiana, is the external contractor for this part of the operation, and she individually inspects every garment. They are all sent back out within two days, ready to be worn again. We process, clean, inspect and repair more than 2,800 sets of PPE every year.”
DECONTAMINATION
Also on site is a decontamination unit, where ambulances can drive in and have the vehicle and crew cleaned thoroughly. While the vehicle and every part within it is sterilised in a two-hour process, personnel take turns to move through the unit and disrobe, shower, and change one by one in a warm, sterile and private cubicle. Anything that can’t be cleaned is disposed of.
“We have never had anyone actually get contaminated, but rather than taking the chance of someone bringing contamination back to their station, or even the psychological side of it, we go through the procedure carefully,” A/S/Off McMenemy tells me. “The fact that it never happens only goes to prove that it is 100% effective.
“Ambulances also come in on a scheduled basis from each station for a deep clean done by Noel Donovan, who is very thorough, taking two weeks to clean every single part.”
While there is so much to do here, the Service Support Centre is seeing an increased workload as new vehicles, equipment and management systems come on board.
CONSTANT IMPROVEMENT
“As well as advancements in our PPE, our drug storage, and monitoring of our equipment, which has been completely updated, we have a continuous cycle of improvement, which we are constantly reviewing. That includes environmental issues, so one of the things we are looking at now is the removal from our supply chain of PFOS foams, which can be environmentally damaging, so we have a two-year cycle where we want to compare it to more environmentally-friendly firefighting foams, which is a big step. That would require taking in every firefighting vehicle, looking at the foam delivery system and calibrating it for an environmentally-friendly foam. This would require a lot of technical work.
“Then we have the new swift water rescue equipment, and this year we have brought in some new vehicles. We have introduced a new Tunnel Response Vehicle, three new Class B fire tenders, we are introducing three new D/O vehicles, a new paramedic vehicle and 4×4 vehicles for challenging weather conditions, so it has been quite interesting, but busy.”
With the increased use of IT, constant modernisation and a dedicated team, the Service Support Centre is able to manage all of this work, which is in itself a remarkable achievement.
The sheer number of responsibilities are a major challenge, but are also rewarding. T/O Guilfoyle says that keeping everything in service operational within financial constraints is difficult. “We need to have a good logistical and financial plan in place,” he says, “but we have a well-oiled machine, and the most rewarding thing about the job is knowing that we have played our part in keeping the operational show on the road.”